Developments in Glass Mold Industry
06.03.2020
Varzene Metal
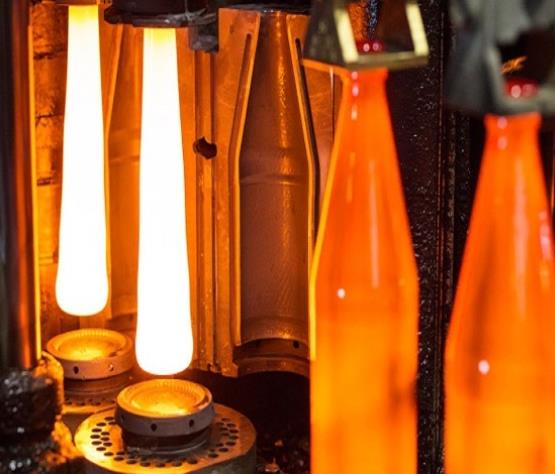
GLASS MOLDS
Molds used in the production of glass packaging shape the product by contacting with high temperature molten glass in the air. Working surfaces of molds that come into contact with molten glass are exposed to mechanical stresses and thermal cycles. Damages on the mold surfaces with these effects limit the service life of the molds and deteriorate the product quality. Among the mold metals that provide the expected properties for glass packaging production, the cheapest and most easily shaped materials are gray cast iron.
Damages in cast iron mold parts occur as a result of the environmental conditions during glass packaging production negatively affecting the mold. Temperature differences caused by high temperatures and rapid cooling create thermal stresses on the mold material. At the same time, the oxidation that occurs at high temperatures disrupts the surface properties of the molds, which affects the product surface quality negatively.
their lifetime is decreasing.
Mold materials used for glass production tend to adhere under high temperature and viscosity conditions and are exposed to tensile forces applied to separate the adhered glass from the mold surface. In studies carried out at high temperatures in an oxidizing atmosphere, great differences in performances have been found due to the interaction of different mold materials with molten hot glass.
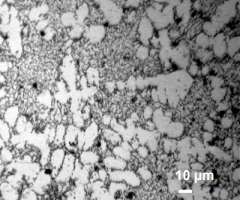
Alloy casting used in experiments microstructure
of the iron sample
Nickel alloys (Inconel 625, Inconel 825, Inconel 925 ...) are preferred in glass molding with their high strength, processing ability and extraordinary corrosion resistance.
Thermal surface coating with self-melting nickel-based alloys plays an important role in the protection of countertops against abrasion in the glass mold industry. Bottle machine tools operate under very severe conditions subject to wear, corrosion and rapid thermal cycling.
The main properties of nickel-based alloys are high wear resistance and good corrosion resistance at high temperatures. This leads to the widespread use of nickel alloys in the glass bottle manufacturing industry for surfacing cast iron parts.
Hardfacing processes with powder welding, flame spraying, HVOF spraying and PTA welding, new molds, pistons, chambers, neck rings, plates etc. uses self-pollinating powder for manufacture and for repair and maintenance.
DEVELOPMENTS IN GLASS MOLD INDUSTRY
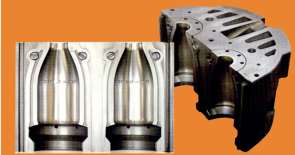
Glass Mould |
|
Plungers
Narrow neck plungers
Best choice |
|
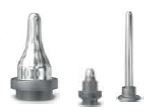 |
|
|
|
|
|
|
|
Mould, mould neck,
mould base, funnel,
repair of mould
Best choice
Bronze moulds incl.
Small repairs |
|
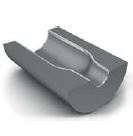 |
|
|
|
|
|
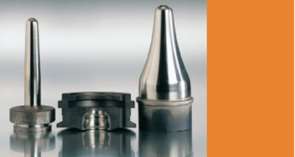
Pistons and neck ring |
|
Bottom mould, bottom plate,
ring, sealer, baffle
Best choice
Bronze moulds incl. |
|
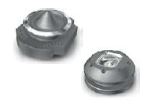 |
|
|
|
|
|
|
|
Blow head, guide ring
Best choice
Bronze moulds incl. |
|
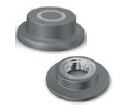 |
|
|
|
|
|
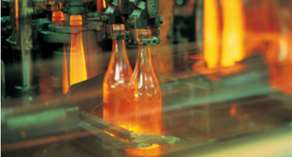
Glass Bottle Production |
|
Neck ring
Best choice
Bronze moulds incl.
Thick layers > 8 mm |
|
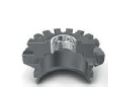 |
|
|
|
|
|
|
|
Holders, support
Best choice |
|
 |
|
|
|
|
|
REFERENCES
• https://www.hoganas.com/globalassets/download-media/sharepoint/brochures-anddatasheets---
all-documents/glass-mould-industry-solutions_may-2017_1949hog.pdf
• https://www.hoganas.com/surface-coating
Alaşımlı dökme demir kalıp malzemelerinin cam ambalaj üretimindeki davranışı
• C. Fahir ARISOY* , M. Kelami ŞEŞEN
İTÜ Fen Bilimleri Enstitüsü, Üretim Metalurjisi Programı, 34469, Ayazağa, İstanbul